Coronavirus: 5 important lessons to boost supply chain efficiency
Learn how dual sourcing and automation can help manufacturing, logistics and warehousing firms with supply chain efficiency.
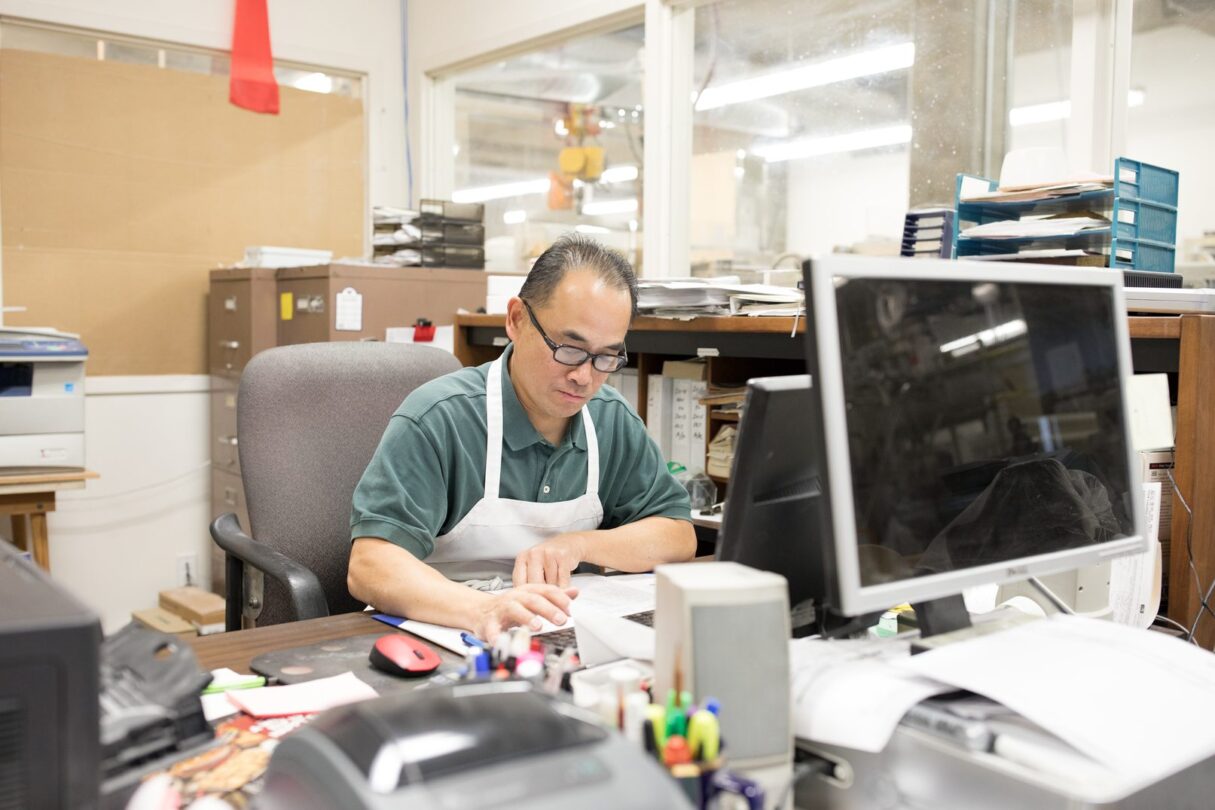
The coronavirus (COVID-19) outbreak has highlighted numerous vulnerabilities in the global supply chain, notably:
- We were unprepared for this particular situation
- The requirements on supply chains are changing daily, and that is proving challenging
- Those changes are not universal – they depend on the sector, consumer sentiment, etc.
Around the world, many governments have been in some way slow to act. However, they’ve done an extraordinary job of pulling together resources where they can.
Despite this, businesses have to recognise that they can’t always rely on government support being in the right place at the right time in the case of truly ‘black swan’ events.
I’ve been in supply chain management for 15 years and academia a further 17 years, and I can honestly say that the industry is exceptionally capable: the bigger manufacturing and logistics firms can usually see trends rapidly enough to react.
They need to be proactive because supply chain efficiency is all about optimising for customer demand. But coronavirus caught everyone flat-footed.
Here are five lessons for the manufacturing, logistics and warehousing industries.
Lesson 1: Digital powers flexibility
In terms of realignment, we’ve seen some extraordinary pieces of work, where large companies have changed their operations almost overnight.
From Walmart to Tesco, and of course the ever-present Amazon, the largest players have not just managed to keep the lights on, they have thrived.
Many wholesalers in individual sectors have successfully developed direct-to-consumer offers where their retailers have shut down, again in a matter of days.
Consumers are still there. That’s the key message: certainly, there is a practical issue around packaging and branding, for example. But people do still want milk.
Now, it’s true that Amazon has deeper pockets than a typical midsize manufacturer, but online shopping has been developing for the past 15 years.
Amazon is certainly a pioneer, but both facing the consumer and facing back into the supply chain, digital tools are now available to simplify and optimise the supply chain across the board.
In fact, a producer today faces a much lower cost to optimise their business than Amazon, which has invested for two decades to build these tools from scratch.
Where suppliers have fallen short is that they have allowed Amazon to capture their markets – indeed that was often true even before coronavirus.
Many commentators suggest that the key output of the current outbreak will be a rapid deterioration in the state of retail.
I would agree with that possibility, but there is a more optimistic view: smart producers and businesses further up the supply chain will realise the value of investing in online channels.
That means not only selling direct to consumers but also optimising upward supply chains for flexibility when dealing with manufacturers and farms.
Lesson 2: Dual sourcing is a priority
Not everybody wants to become an online retailer, which brings us to dual sourcing.
Perhaps the greatest lesson for supply chain professionals here is that we have focused so exclusively on leanness that it has made us blind to the importance of resilience.
I believe wholeheartedly in global trade and global supply chains.
Globalism is better for business than protectionism and global trade fundamentally makes the world a better place – for businesses, consumers and whole economies.
But supply chain experts then also must keep their eyes open to the world in which they find themselves.
The painful truth is that the coronavirus outbreak was not completely without warning to the rest of the world.
In February 2020, China used significantly less energy than the same time the previous year.
Also in the same month, the port at Long Beach in Los Angeles saw a significant reduction in the number of container vessels coming from China.
There were signs of trouble ahead.
Larger businesses – and the smaller ones who partner with them, if communication was strong enough – could and should have noticed problems on the horizon. More importantly, they should have had a Plan B for alternative sourcing from other parts of the world.
I think that in a restructured vision of commercial supply chains, we will see many more businesses shoulder the cost of secondary channels, rather than putting all their eggs in one basket.
And while China has traditionally been the least-cost supplier of choice such that this outbreak really emphasizes the issue, economic, geopolitical and social problems can develop anywhere.
It’s crucial that businesses can flex to alternative sources.
Lesson 3: We are in a transitional period – the ‘new normal’ is a way off
Governments want and need the economy to return to some semblance of normality, and they will encourage businesses to work out their operational needs.
Right now, companies are wrestling with the day-to-day challenge of how to protect employees when they come into the workplace, particularly:
- The availability of personal protective equipment (PPE).
- How to organise for social distancing where people might have previously operated in close confines.
- How to create a testing regime when tests become widely available.
These can be particularly challenging in labour-intensive parts of manufacturing and logistics, from food production to warehousing and distribution.
Only then will companies be able to raise their eyes towards the long term.
But where I’m optimistic is that businesses will naturally aim to flex, initially for survival, but ultimately to find opportunity.
That will include:
- Working from home for a large number of employees, many of whom (although by no means universally) are finding personal benefit in the change, too.
- Omnichannel retail, which means both traditional retailers embracing digital and wholesale/supplier organisations joining the direct-to-consumer market.
- A significant restructuring of business, particularly to focus on core activities, with a shorter timeline of strategic visibility and less speculative activity.
Lesson 4: The medium term will be challenging
Here is what I think we can expect in the medium term:
Protectionism
Less positively, as a globalist, I think we will see new types of protectionism, often driven by political sentiment rather than the facts, which will shorten supply chains.
For example, some countries will want to protect their food sources by growing more at home. This will mean changes for logistics businesses in the medium term.
Fewer people travelling will mean less freight, too
Travel will take several years to return to 2019 levels and this will also affect global supply chains. When we travel less, we do fewer deals and operate closer to home.
Furthermore, most people don’t know that passenger planes carry plenty of cargo, too. So the inevitable reduction in passenger flights will take its toll on commercial cargo.
Higher costs
We also need to realise that the base costs of transportation and logistics are going to go up. That may be mitigated by new efficiencies, but again, it will mean change and disruption.
These are just a few of the effects. Every business should be re-examining its supply chain and truly understanding it because supply chains are granular and intricate.
Test for vulnerabilities and understand the impact of these and other factors.
Lesson 5: Embrace automation
The prognosis had always been that we would see automation truly impact logistics by around 2030; and major players in the space have been moving down the automation, artificial intelligence (AI) and robotics paths for a decade or so.
Now, if you have a situation where people are not permitted into a workplace, that will inevitably turn minds to the value of automation.
Automation ceases to be a way to shave a few percentage points off operational costs; it becomes a financial imperative, either to keep the business going, or to shore up competitiveness.
And one of the big arguments against automation – that the cost of deployment is greater, at least in the short term, than paying employees – falls out of the equation.
I therefore think that supply chain professionals will look back in a couple of years and see coronavirus as a clear stimulus for the acceleration of automation in logistics.
Add to that the rapid improvement of capability in autonomous vehicles and I think logistics will look different in five years, not 20.
There is unquestionably a societal cost there. It may cost jobs, but if I can say one consistently positive thing, it’s that supply chains are populated by problem solvers.
We have the world’s most flexible and opportunistic people. We will get through coronavirus just as we have got through every other shock to the system.
Final thoughts
I hope we don’t lose our global outlook because that would be a real shame.
But as an industry, I’m hopeful: disruption teaches us lessons, and those lessons – dual sourcing, inventory flexibility, and so on – will feed strategies for everyone moving forward.
Coronavirus and your business
We’ve gathered information and resources to help navigate this situation. You can also find out about support for Sage solutions, including enabling home working.
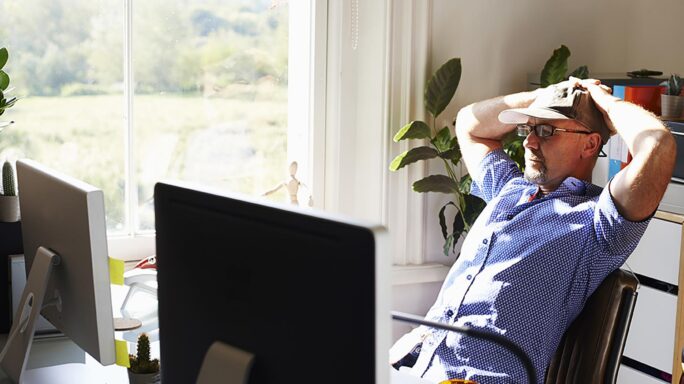
Ask the author a question or share your advice