COVID-19: Why South African Manufacturers should reconsider their supply chain
As the South African lockdown lifts and manufacturers restart operations, how can they optimise the supply chain and restore resilience after COVID-19?
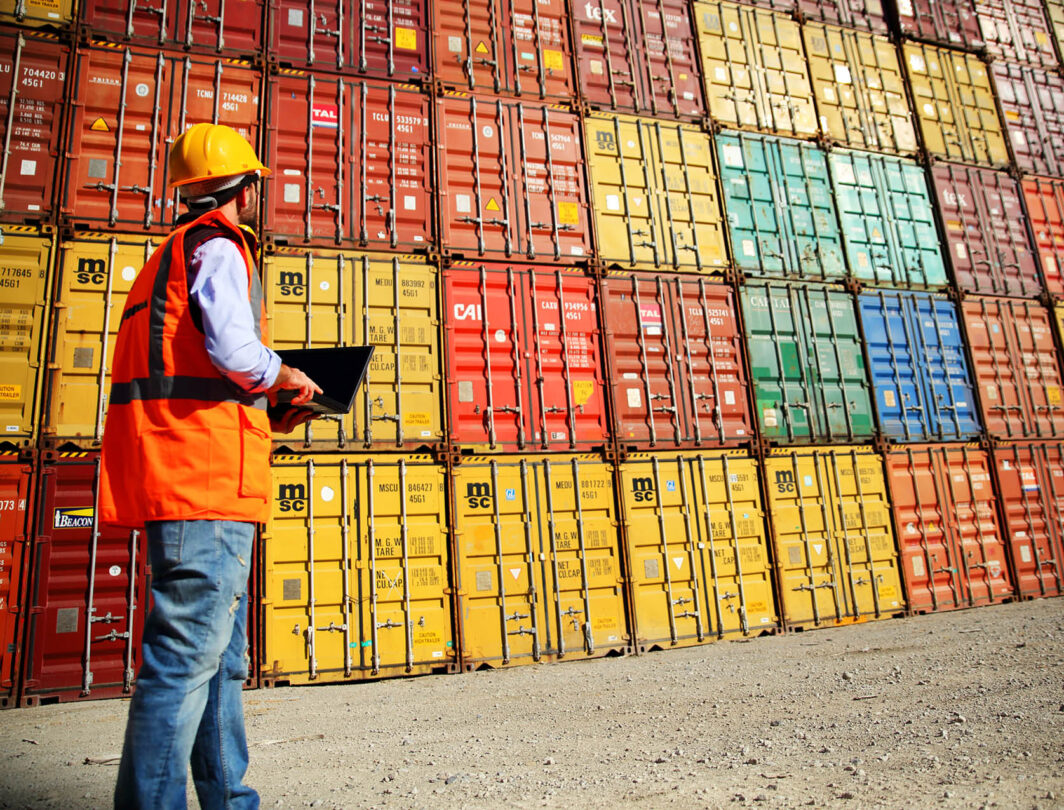
Like most industries, South African manufacturing has been impacted by COVID-19. As global supply chain disruption has exposed many challenges – for instance, being unable to source enough personal protective equipment to meet the rising demand – some manufacturing companies are now looking for innovative ways to optimise.
We spoke to Tracey Linnell, director of specialist risk and resilience consultancy firm Morgan Solus, who shared ten tips for your business.
1. Know your risks
Linnell first noticed issues caused by COVID-19 in late January, although at this stage it was only impacting manufacturing companies that sourced stock from the Far East. One month later and many more companies were feeling the impact. This led to concerns about how a significant, unexpected shock to global supply chains could have a domino effect on other companies in markets across the globe.
“At the beginning of the year, people were mostly focusing on what we can call Tier 1 supply chain risks,” Linnell says. “This meant that the initial supplier review only looked at the circle outside my circle. But because the world is so inter-connected, the components that you’re sourcing might come from three layers below your primary supplier. That’s why it’s now about taking a tiered approach by understanding who your suppliers are and who their suppliers are.”
2. Map your entire manufacturing supply chain
Understanding who your suppliers are and how they are connected is critical for manufacturing companies navigating COVID-19. That starts with making a list of your most critical suppliers, identifying where they’re based, and knowing how anything that impacts them (from natural disasters to political instability) might impact you.
“Manufacturing companies need to know things like which supplier is going to be impacted based on geography, the mode in which products will be shipped, and what the impact will be when things go wrong,” Linnell says. “But because the knock-on impact is felt in multiple layers in the supply chain, I think there’ll be quite a bit of Tier 1 to Tier 3 supplier mapping post-COVID.”
3. Build a diverse network of suppliers (especially local ones)
Once manufacturing companies have done the mapping, it might be clear that they’re too reliant on specific suppliers or specific regions. This is when they can consider ‘multi-sourcing’ from different people and places to avoid any additional risks. (It’s much like consumers might have a back-up store to get products they need.)
“As COVID-19 started to rear its ugly head, we began to feel the impact locally because of the physical stock that was coming out of the Far East,” Linnell says. “That was a known risk that started to affect the supply chains for a lot of companies in South Africa. Some companies (prior to any kind of actual lockdown happening) started sourcing locally instead, trying to quickly find South African companies that were selling the same product. So that was one of the strategies.”
4. Follow due process in procurement
Under normal circumstances, it takes time for manufacturing companies to onboard new vendors. But in the world of COVID-19, some companies were so desperate to get stock that they were partnering with suppliers that put them at risk. In some cases, there was negligence that caused quality control issues or outright fraud that cost companies (and governments) millions.
“In certain companies, you’ve either had an impact from the supply side – in other words getting stock in – or you’ve had an impact on the demand side,” Linnell says. “For some of the pharmaceutical companies, there’s obviously been a massive demand for supplies (masks, ventilators, and so on). But they couldn’t keep up with the demand for what was required so they were looking for multiple suppliers all over the place. Unfortunately, breakdowns in the procurement processes were inevitable.”
5. Plan for business continuity
To avoid this kind of disruption during the COVID-19 pandemic, manufacturing companies should do more detailed research into their suppliers. This is a normal part of business continuity planning but it must be even more detailed right now. It’s about knowing who your suppliers are, what products or services they provide, and how dependent you are on them. Once you’ve ‘risk rated’ them, you can put mitigating controls in place.
“Look at various strategies for your different suppliers based on products, services, and risk exposure,” Linnell says. “If it’s a critical single source supplier – in other words, I can only get a component from them and not from anyone else – then typically we put in place service level agreement clauses that stipulate that the vendor must make an alternate plan to ensure services to the organisation. We also send out letters to them, asking to confirm availability and their COVID-19 plan. Once they’ve supplied that information, we can understand the broader impact.”
6. Consider incidents holistically
If a supplier can’t meet their agreement, due to COVID-19 or any other reason, it’s important to know this. Unfortunately, many manufacturing companies have an issue with reporting. They might register an incident but not be able to fully understand how it impacts the entire business.
” We’ve seen many manufacturers struggle with this issue over the last couple of months,” Linnell says. “For example, if a manufacturing company has a raw material issue, it tends to stay in that department. It doesn’t get aggregated up or escalated as a risk. Worse, companies are reverting to archaic Excel-based reporting when they should be using more advanced supply chain mapping software that can depict the interdependencies.”
7. Understand new technology
Indeed, with all the advancements in technology – from big data and artificial intelligence to advanced analytics and the ‘Internet of Things’ – now is a great time for companies to learn about the new tools that could make things easier during COVID-19 and beyond.
“From a technology perspective, the one that seems to be popping its head up is blockchain,” Linnell says. “In the pharmaceutical space, Pfizer’s gone into a conglomerate with other companies and created a blockchain solution called MediLedger. It allows everybody to have access to the blockchain, which nobody can control as a single company. But what they can do is verify stock and authenticity from each of the participants. Obviously it requires that everybody broadly adopt blockchain technology but that’s one of the future strategies that we might see coming out of COVID-19.”
COVID-19 Business Advice
We are here to support you during this time.
We’ve gathered information and resources to help navigate this situation. You can also find out about support for Sage solutions, including enabling home working.

8. Embrace new technology
Once manufacturing companies understand the potential for using new technology, it’s important for them to make the transition. The sooner this happens, the sooner the company can better manage its risks. Indeed, there’s likely to be a demand for professionals who specialise in data analytics and who can help drive this change towards new technology, during COVID-19 and beyond.
“DSV, a major player in transport and logistics has invested heavily in technology in the last couple of years,” Linnell says. “And so their supply chain, particularly when you look at the warehouse in Modderfontein, is highly automated. Similarly, logistics companies that are technology adopters use what’s known as a ‘digital control tower’, where the team sits in an office with all the technology. Meanwhile, the actual movement of stock happens through automated machinery.”
9. Be open in your communication
Although many manufacturing companies see the benefit in these technologies of tomorrow, many are simply focused on getting through today. And while many have been good at crisis management due to COVID-19, others have room to improve.
“During the lockdown, a lot of it has been about communication to interested parties to inform them of what can and can’t be done,” Linnell says. “But it’s not just about getting stock in or getting services out. It’s also about outbound communication to customers. At the end of the day, a business has to serve the customer. If you can’t keep the customer happy, they’ll go elsewhere.”
10. Prepare for challenges beyond COVID-19
When COVID-19 first began spreading in the Far East, people didn’t expect it to migrate so quickly or affect the world so intensely. Indeed, there wasn’t much preparation in place for South African manufacturing companies. But even though many are now adjusting to the new normal (for example with ‘dark warehouses’ to split stock in different areas to avoid a total shutdown in case an employee is infected) companies need to prepare for the future and build resilience ahead of the next wave of disruption.
“We’re living in a volatile world,” Linnell says. “So the likelihood of another impact to supply chains happening in the next twelve months, whether it’s COVID-19 or not, is high. With our clients, where we’d already done the pre-work, the risk was low because we knew what the answers were and how we were going to manage. But the companies that have struggled have been the ones that tried to manage it on the fly.”
Conclusion
In conclusion, now is the time to get more serious about conducting a detailed supply chain audit – not just a theoretical tick-box exercise but one that involves proactively ensuring that you have the right plans in place. But if you aren’t prepared for the next major disruption wave and have no mitigation strategies in place, your business may not recover.
What technological advancements can be invented to help manufacturing companies survive the effects of Covid-19