Trends & Insights
Robotics in logistics: 4 key trends to be aware of in the coming year
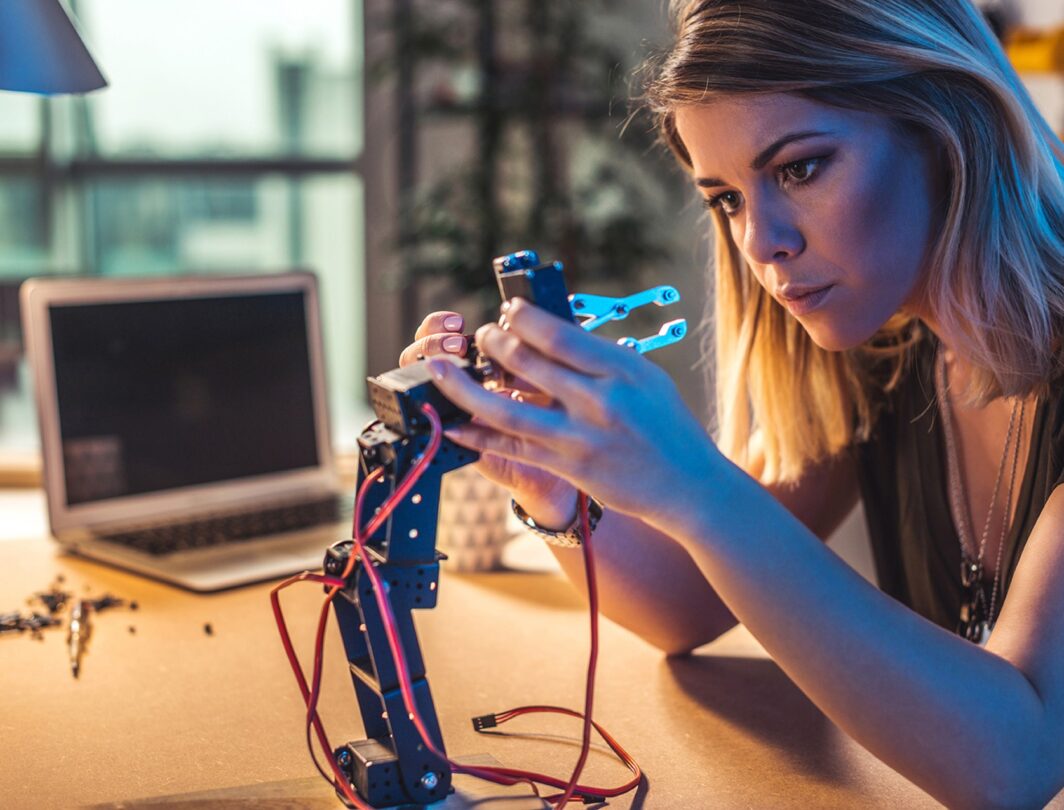
Back in 2017, artificial intelligence (AI) specialist venture capital firm Loup Ventures suggested that the industrial robotics business will have grown to $33.8bn (£26bn) by 2025.
By 2019, analysts IDC had upped the ante, posting a valuation on the sector of $53nb (£40.7bn) by 2022. The robots are definitely coming, so what can we possibly expect to see from robotics in logistics in the next 12 months?
1. Robots achieving human levels of manipulations
Robots have always been capable of basic manipulations – especially repetitive actions (picking up objects from pre-defined positions, executing a movement or manipulation and repeating the cycle).
To add transformative value in speed, efficiency and replacing humans in boring jobs, the next 12 months should see a point where robots with more human-like capabilities become tantalisingly affordable.
Something as simple as identifying and picking the right object from a pallet in which, say, some boxes have fallen from the stack, is something a human can instinctively understand, but which is a dramatic step forward in ability for a robotic arm.
Jim Liefer, former CEO of Kindred Robotics, said in an interview with Supply Chain Brain: “The trend is definitely moving to direct manipulation of physical product.
“By that I mean robots that understand unstructured themes, where to pick something up, how to identify it, and how to place it.
“That, I believe, is where everything’s going… AI is the key. It has enabled robots to work in a world full of exceptions — an environment that’s unpredictable.”
Action: Think about what robotics is on the cusp of achieving and invest there, not in yesterday’s technologies. Prioritise interoperability and ongoing upgradeability.
2. Robots will allow people to work on more useful tasks
The “robots want your job” refrain isn’t backed up by experience. The coronavirus (COVID-19) pandemic has made the economics of robotics more attractive and social distancing has reduced the number of people on production lines. But few will simply lose their jobs – they’ll be needed elsewhere.
“As the economic and social effects are expected to last long after the primary health concerns have been abated, manufacturers are likely to continue reshoring their supply chains and operations,” Patrick Sobalvarro, CEO of Veo Robotics, told Supply Chain Dive.
Inshoring and reshoring (among other industry trends) will keep humans busy for a while yet.
Robotics is focused on allowing people to do more useful and less repetitive and error-prone tasks. Plus, the modern logistics environment is already incredibly efficient already, with people only deployed for complex manipulations.
In many warehouses, there isn’t a particularly large labour pool to swap out.
Perhaps the most important voice globally in supply chain robotics is Melonee Wise, CEO of Fetch Robotics.
She says: “Robots will one day be a common site in logistics, doing the heavy lifting and travelling the long distances to let people do more meaningful tasks.
“What will success look like?
“When robots empower people and enable those who know nothing about computers or robots to operate them.”
So people will be employed more usefully, and it’s the human-to-robot interface that needs to be improved – particularly as we will spend far more time working alongside, rather than removed from, robots on tomorrow’s production line.
Assembly Magazine estimates that “manufacturers could be wasting nearly $90,000 per year on each operation that requires the use of collaborative robotics, due to improper, insufficient or even non-existent integration of the robots into their processes”.
Action: Think about the processes you expect robots to help with, and what contribution they’ll make to your bottom line, both today and in an ideal world.
Put a value on the labour that robotics will free up by understanding where else individuals can be gainfully employed – because in most cases, you’ll gain greater value from redeploying their latent knowledge and skills than letting them go.
3. From piecemeal to platforms and platoons
Platoons of robots working in sync are vastly more effective than individual units, and the ecosystems (open standards, cloud connectivity, etc) to allow robots and vehicles to work together are a priority for the coming years.
Innotech Today says: “Everything is becoming integrated. Robots are not an exception. Expect more cloud software to become available that allows your robots to work together.
“Centralising everything into one platform will allow your robots to work more efficiently and get more done.”
But none of this is easy to predict.
There’s little interoperability in robotics today. Top-level standards such as (the gloriously named) O-MI should enable messaging between everything from Internet of Things (IoT) devices to autonomous vehicles.
But in-warehouse systems are currently under no pressure to interface with competitors or other systems. Indeed, it’s likely going to be the role of enterprise resource planning (ERP) to connect these new classes of data source in the interim.
Action: Robotics vendors are understandably keen to sell whole fleets, and you have many options in this respect.
Lagging a couple of years behind are the platforms that will enable interoperability and improve the way robots can be customised and repurposed (and therefore the longevity of a robotics investment).
4. Filling out the market
There’s a trade-off in the robotics business (as with many businesses) between price and complexity. Generic robots are cheaper and easier to repurpose but may be harder to program and never as effective as a specialist unit.
Conversely, more applied robots will be expensive, but better at a specific job.
These trade-offs will become more apparent as the market fills out with generalist and specialist robotic solutions for an increasingly wide range of niche needs.
For an example of a robot doing a great job of ‘heavy lifting’ (literally), take a look at Boston Dynamics’ Handle, which can neatly stack pallets from multiple SKUs, left alone in a warehouse.
Locus Robotics’ multi-bot system, meanwhile, promises to double warehouse productivity with bots designed to work with and around people.
Both perform best in highly structured environments.
Then there’s Fizyr. It’s much slower in action, but that’s because it’s capable of picking items in completely unstructured situations (such as a pile of product in a bin).
The use cases are wildly different and we’re likely to see a wide range of startups from the commodity end of the market all the way through to deeply bespoke.
Why now? One word: Amazon.
Back in 2012, the ecommerce behemoth purchased Kiva, the then leading logistics robotics firm, leaving a sizeable dent in the talent market.
Fast forward to 2019-20 and a raft of seedling startups have sprung up to fill the gap left by Kiva.
Some have reached maturity, one example being 6 River Systems, which was bought by Shopify in 2019. In its wake are logistics specialists such as Geek+, Vecna and Clearpath.
Action: Assess the market. The logistics robotics sector is as vibrant as it has ever been – and with heavy investment comes both risk and opportunity.
Ask the author a question or share your advice